3D Printing is creating a physical object from a digital 3D model by adding material layer by layer. This technique is typically used to make plastics and metals.
3D Printing is revolutionizing how manufacturers do business, from rocket nozzles to custom shoes. It also inspires young students and helps them find new careers in STEM fields. Contact By3Design now!
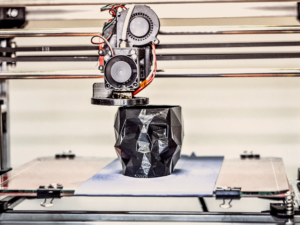
3D Printing allows for faster production times and helps to reduce project lead time. This can be especially beneficial for projects with tight deadlines or when the quality of a prototype cannot be compromised. In addition, reducing the number of layers required in a print can significantly speed up the process. By focusing on improving 3D printer technology and optimizing printing settings, it is possible to achieve higher print speeds without sacrificing quality or precision.
While many consumers and manufacturers have embraced 3D Printing, its full potential has yet to be realized. As the technology continues to advance, it is poised to transform manufacturing processes and reshape how businesses operate. From rapid prototyping to full-scale production, 3D Printing is making its mark in industries across the United States and worldwide.
With this new technology, you can quickly produce models or jigs to test and refine products before larger manufacturing runs. This can save money on costly mistakes and ensure that a product is ready for market. It also eliminates the need to store or purchase large inventories of finished goods, resulting in significant cost savings.
Another advantage of 3D Printing is its ability to create bespoke components for existing or new products. This can be used for everything from a custom fit on medical implants to replacement parts for cars, airplanes, and trains. The rail industry has already taken advantage of this capability to create bespoke rail couplings, housing covers, and arm rests for drivers.
A common method of 3D Printing–extrusion–starts with a polymer rod called filament, which is heated, melted, and forced through a nozzle in a printhead. Instructions tell the printhead where to lay down the polymer, forming each layer of the final free-standing 3D object. Each layer is deposited on top of the previous one, creating the desired shape bit by bit.
In the past, accelerating the printhead’s movements has been essential to increasing print speed, but this approach can lead to errors in the printed object. The repeated accelerations cause the printhead to vibrate, resulting in uneven surface finishes and weaker prints. Researchers have recently developed a new printhead that can modulate the rate at which the filament is extruded, avoiding these issues.
Better Quality Prototypes
The accuracy, versatility, and quality offered by 3D Printing make it a cost-effective alternative to traditional manufacturing processes. Using this method, companies can easily iterate designs with little risk of cost or time investment. This flexibility allows companies to improve their products quickly and competitively, increasing sales and customer satisfaction.
In addition, 3D Printing enables companies to display a physical prototype to customers and investors, reducing the possibility of miscommunication and lost information. Seeing and touching a prototype also makes it easier for potential customers to understand the functionality and benefits of a product.
Using this technology, engineers can create complex geometric parts in less time than traditional methods. This can speed up the design process and enable more iterations, resulting in better-performing and more durable components.
Additionally, 3D Printing offers greater flexibility than other manufacturing techniques by allowing for the production of small batches of custom-made parts. This reduces inventory costs and delivery times while boosting overall productivity.
Depending on the type of printer and material used, different types of prototypes can be produced in a range of resolutions and finishes. SLA is ideal for creating aesthetically-pleasing prototypes and visual models, while MJF produces stronger and more durable parts than FDM. Photopolymers are used in SLS and MJF, which offer high-resolution and smooth surface finishes. These materials are expensive compared to FDM, however, and require extensive post-processing to maintain material properties.
FDM is best for constructing functional prototypes, as it can produce durable, accurate parts with good mechanical properties. In addition, this method is cost-effective and suitable for low-volume manufacturing. FDM is used by many automotive manufacturers and aerospace companies to produce vehicle body parts, powertrains, and aircraft wings.
The most common problems associated with 3D Printing are related to the printer’s build size, print speed, and print quality. To avoid these issues, it is essential to optimize your printer’s settings and implement comprehensive testing protocols to ensure a high-quality product.
In addition, it is a good idea to use lightweight materials, as they can save on the cost of production. Other important considerations include avoiding unnecessary support structures and designing parts to minimize material use. Avoiding unnecessary supports can significantly reduce printing time and costs, while minimizing material use can help to increase print strength without sacrificing quality.
Reduced Costs
With the expiration of key patents, innovation and competition have brought prices down considerably, making 3D Printing more accessible to small businesses and hobbyists. In fact, a person successfully walked with a 3D printed one-piece prosthetic leg in 2008. Other factors also contribute to the affordability of 3D Printing, including the use of readily available materials, such as low-cost plastic polymers and concrete and the absence of the cost of a mold.
Manufacturers can further reduce costs with 3D Printing by using part consolidation techniques, optimizing designs and minimizing the need for support structures. Part consolidation involves combining multiple components into a single, integrated piece, saving on assembly time and reducing the amount of material needed to make the product.
3D Printing also minimizes material waste by utilizing an additive process, which builds the object layer by layer, rather than removing or whittling away excess material like traditional manufacturing methods. In addition, many 3D printers can print with only the raw material required to make the final product, further reducing waste.
The best 3D printing service providers offer a range of materials to meet any project needs and budget, from the strongest and most durable metals for automotive and aerospace applications to bio-compatible materials for medical and healthcare applications. Additionally, 3D Printing allows for the creation of composite materials, such as carbon fiber, Kevlar and fiberglass strands that combine strength with lightweight properties, offering a great alternative to aluminum for critical applications.
Because of the wide range of materials available, it is possible to create any item that can be made through a mold, such as tools, electronics and consumer products. 3D Printing can also make it much easier to produce replacement parts and to customize products to better fit the end user.
For these reasons, many manufacturers begin with outsourced 3D printing services before investing in their own equipment. Even businesses with their own printers rely on outsourcing to expand capacity, access specialized materials and speed up production. The right 3D printing service provider offers industry-leading manufacturing expertise, tight tolerances and on-demand manufacturing to help businesses stay competitive in the market.
Increased Efficiency
As a result of advancements in linear motion systems, high-resolution Printing allows for more precise layer-by-layer material deposition. This increases print accuracy and allows minute details and complex geometry to be faithfully recreated. This, in turn, cuts printing costs by eliminating wasteful over-printing and minimizing calibration procedures.
Because 3D Printing doesn’t require a traditional manufacturing setup (such as injection molds), it’s one of the most agile production technologies available. This enables manufacturers to produce a variety of different parts on-demand, greatly reducing the need for inventories and storage, which can cut into a company’s bottom line.
3D Printing also uses less material than CNC machining and other subtractive manufacturing methods. This is because the printer places filament only where it’s needed, unlike other processes that remove materials from a part. This not only saves on production costs, but it also saves on material disposal and transportation costs.
Moreover, a printer only needs to be operated by a single person, unlike a traditional manufacturing plant, which requires specialized labor for each step of the process. This, in turn, slashes labor and operational costs.
Energy Efficiency
Much of a traditional manufacturing plant’s energy is lost in the form of excess heat, but thanks to improvements in linear motion systems, 3D printers can be used to create components and devices that improve a factory’s energy efficiency. This can include everything from heat-retention materials for machine cooling to parts designed to reduce the amount of power used in a production process. This, in turn, can lower a manufacturing facility’s electricity and fuel consumption.